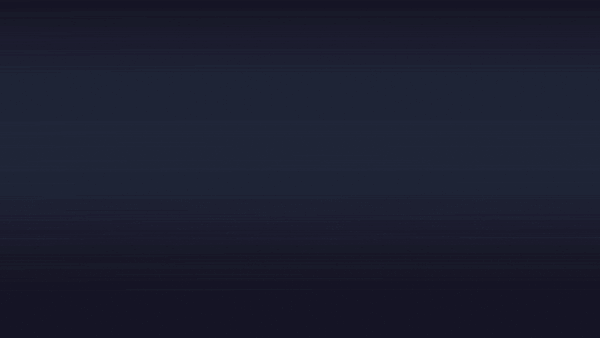
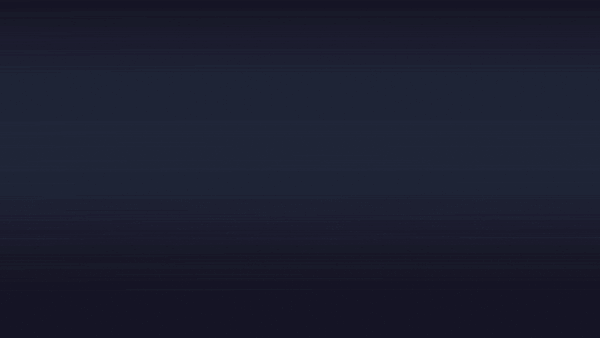
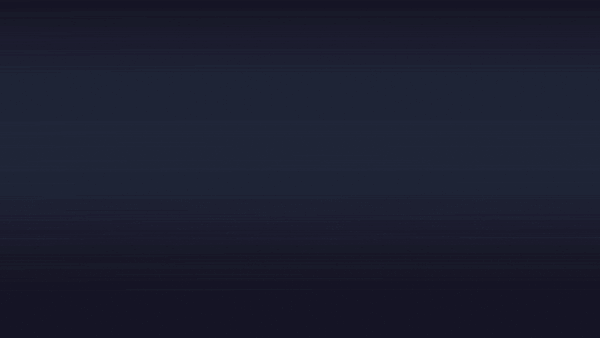
Check out what’s new and the latest training schedule in our Learning Calendar 2022.
New programmes are available to enhance your technical competency and to unleash your potential.
More and more of INSTEP programmes are now HRD Corp Claimable; stay tune for the rest of the programmes.
PETRONAS Edition Learning Calendar
(For PETRONAS staff only):
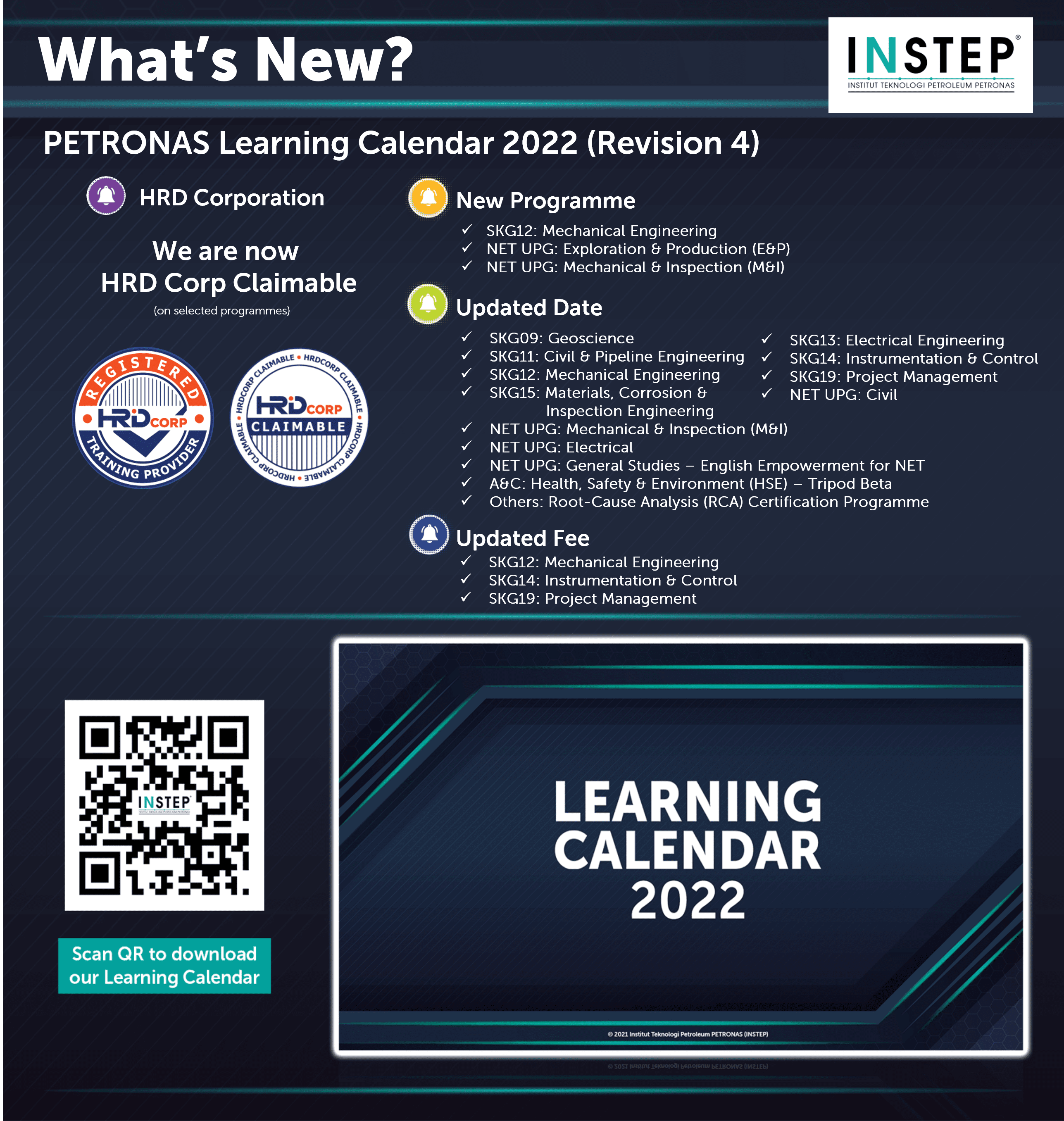
Public Edition Learning Calendar
(Open to all):
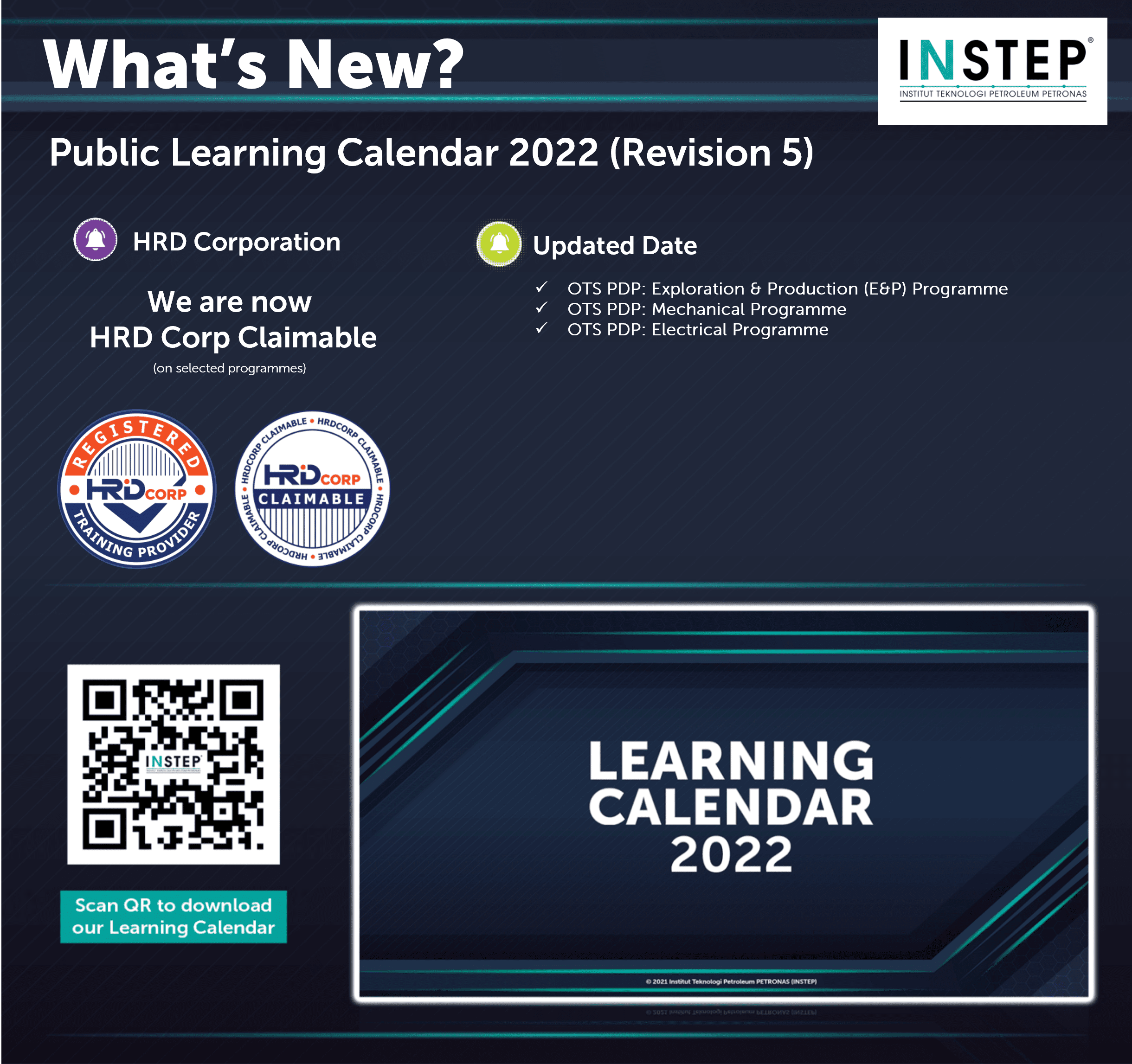
Don’t miss out and join us to upskill yourself in Operations, Maintenance and Health, Safety & Environment Programmes.
So what are you waiting for? Download your copy of Learning Calendar today!
Click here to download:
PETRONAS Group Calendar (Revision 4)
Public Group Calendar (Revision 5)
Reach us at instepmarketing@petronas.com, we would love to talk with you!
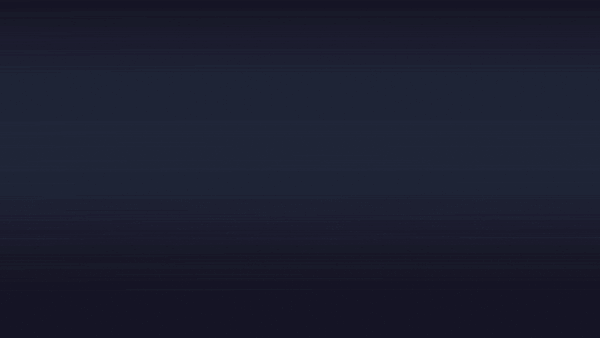
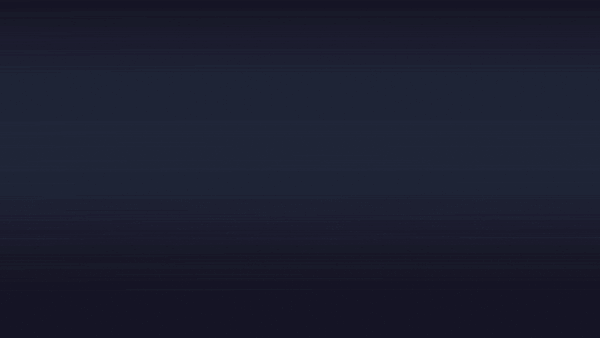
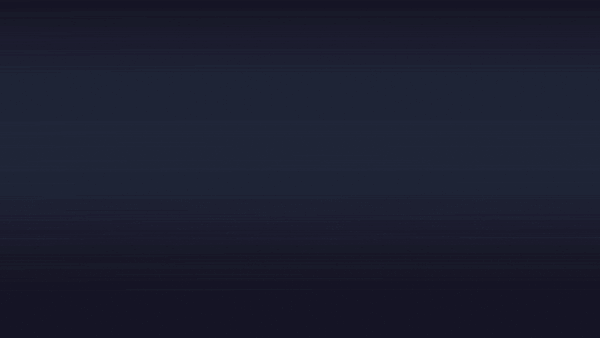
Check out what’s new and the latest training schedule in our Learning Calendar 2022.
New programmes are available to enhance your technical competency and to unleash your potential.
More and more of INSTEP programmes are now HRD Corp Claimable; stay tune for the rest of the programmes.
PETRONAS Edition Learning Calendar
(For PETRONAS staff only):
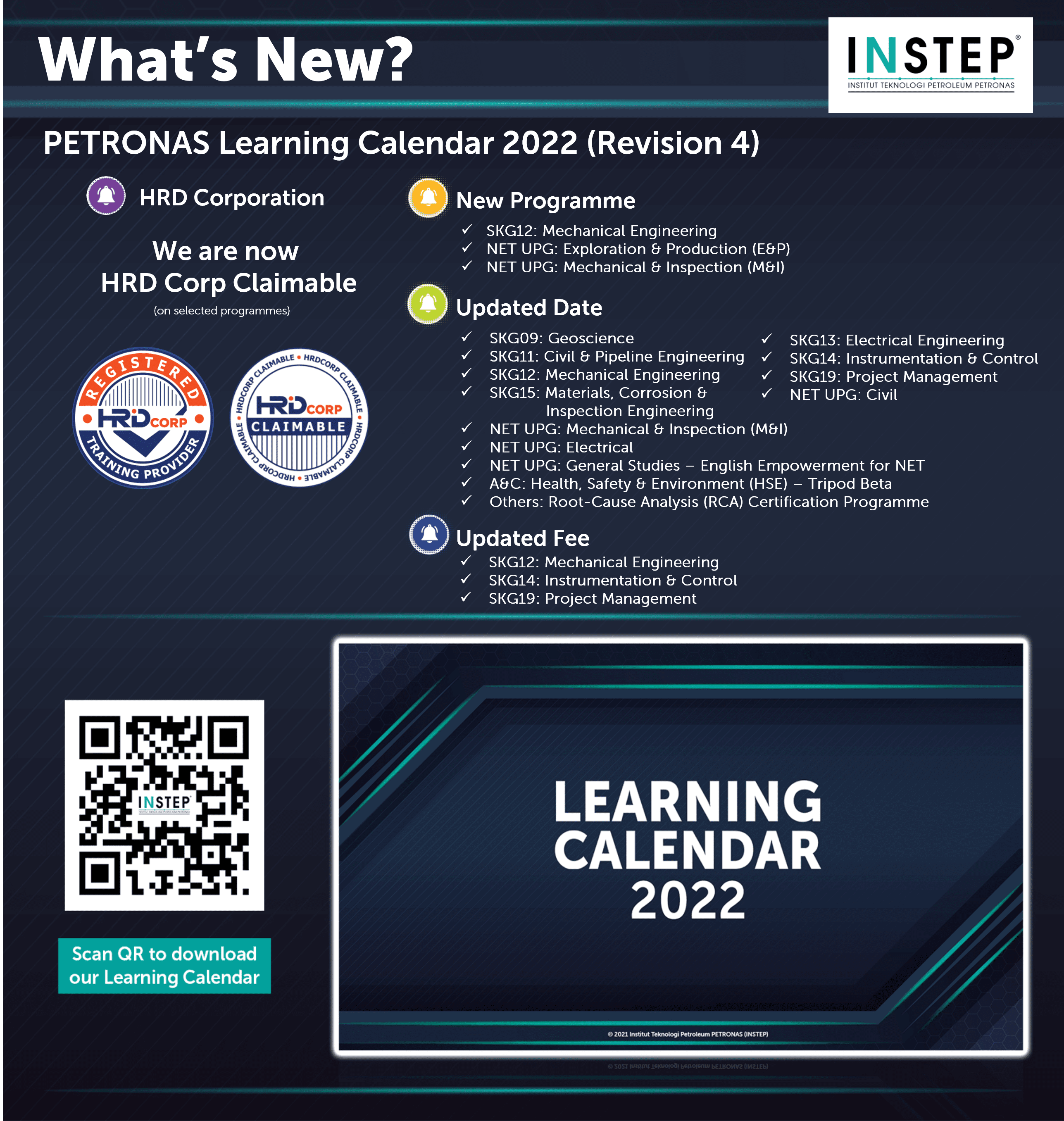
Public Edition Learning Calendar
(Open to all):
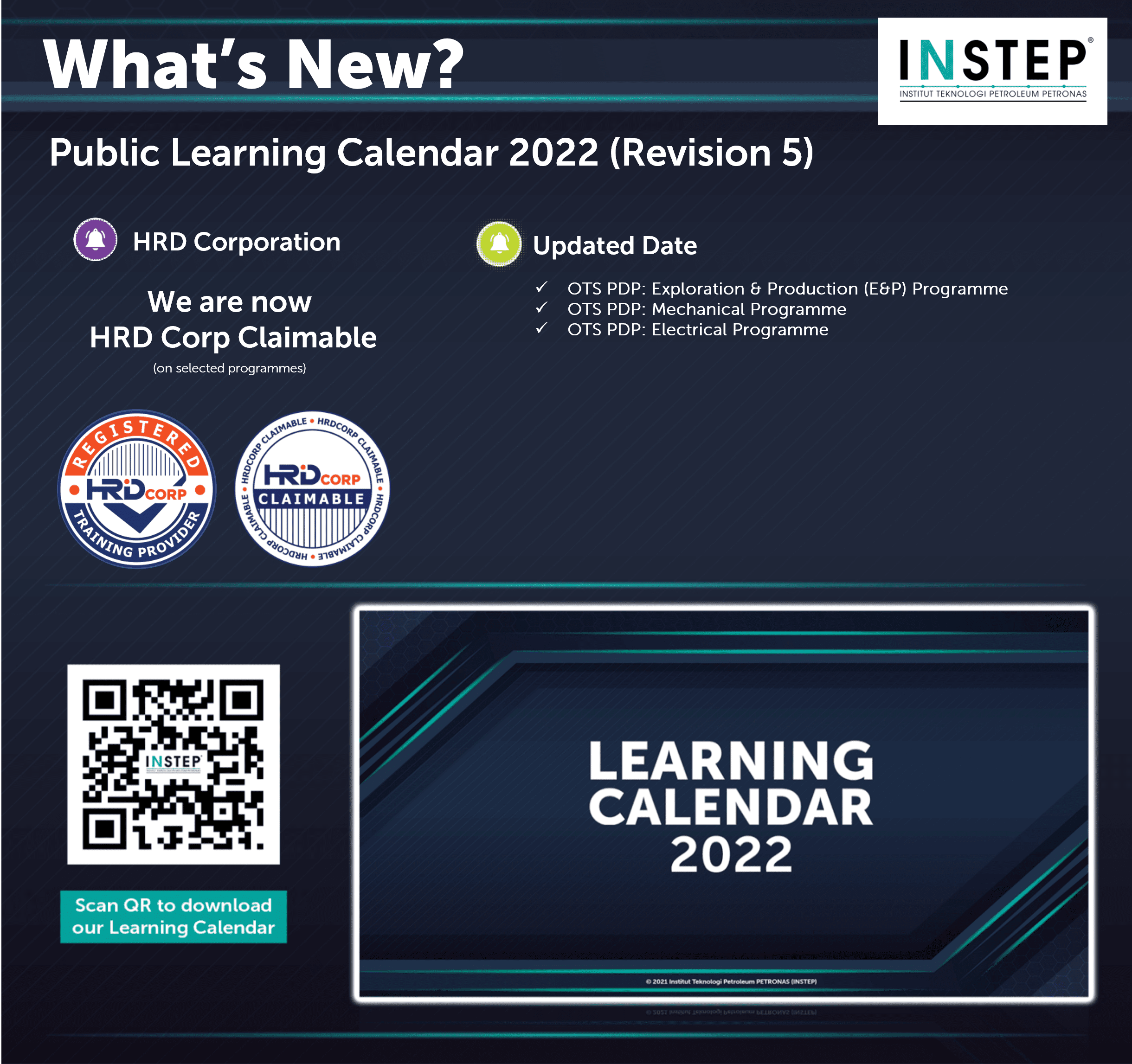
Don’t miss out and join us to upskill yourself in Operations, Maintenance and Health, Safety & Environment Programmes.
So what are you waiting for? Download your copy of Learning Calendar today!
Click here to download:
PETRONAS Group Calendar (Revision 4)
Public Group Calendar (Revision 5)
Reach us at instepmarketing@petronas.com, we would love to talk with you!